Injection moulding is a cornerstone of modern manufacturing, allowing businesses to produce high-quality, intricate parts with precision and efficiency. As technology evolves, modern injection moulding machines offer advanced features that can significantly enhance production efficiency. In this comprehensive guide, we’ll explore how to optimize production efficiency using these cutting-edge machines, ensuring you stay ahead in the competitive manufacturing landscape of 2024.
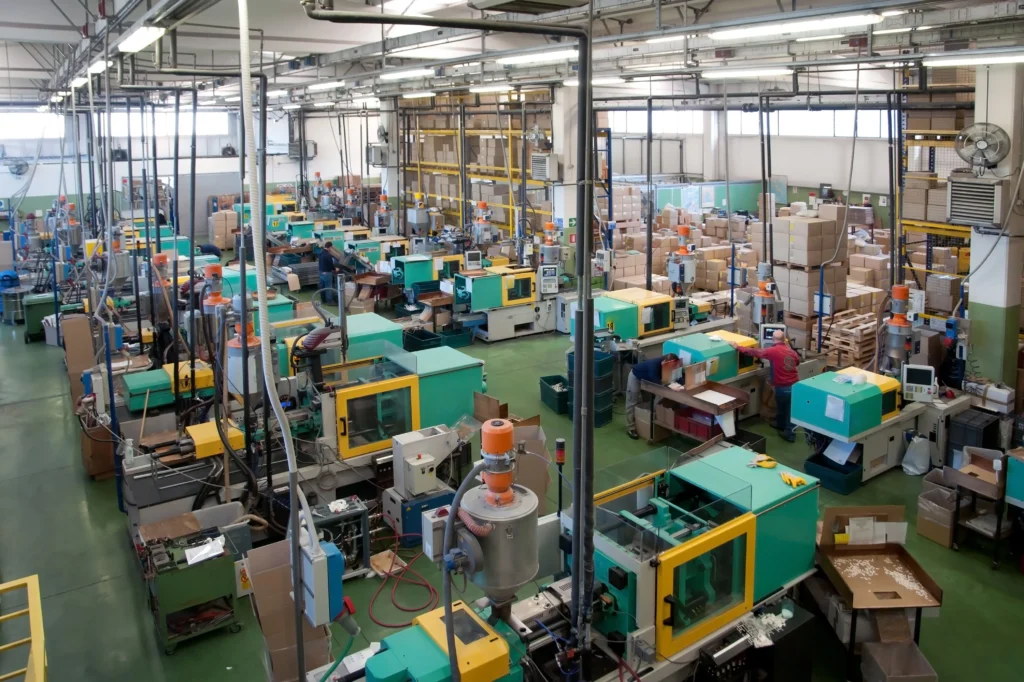
Understanding Injection Moulding
Before diving into optimization strategies, it’s essential to grasp the basics of injection moulding. This process involves injecting molten material, typically plastic, into a mould cavity to create various parts. Once the material cools and solidifies, it takes the shape of the mould, resulting in high-precision components suitable for a wide range of applications.
Key Components of Injection Moulding Machines
- Injection Unit: Melts and injects the material into the mould.
- Clamping Unit: Holds the mould in place during the injection process.
- Mould: The cavity that shapes the molten material into the final product.
- Hydraulic System: Powers the movement of the injection and clamping units.
- Control System: Manages the machine’s operations, including temperature, pressure, and cycle time.
The Benefits of Modern Injection Moulding Machines
Modern injection moulding machines come equipped with advanced technologies that offer several benefits:
- Increased Precision: Enhanced control systems ensure tighter tolerances and better part quality.
- Faster Cycle Times: Improved heating and cooling systems reduce production times.
- Energy Efficiency: State-of-the-art machines are designed to consume less energy and reduce operational costs.
- Automation Capabilities: Integration with robotics and automation systems increases production speed and consistency.
Strategies to Optimize Production Efficiency
Optimizing production efficiency with modern injection moulding machines involves several strategies, each aimed at enhancing different aspects of the manufacturing process.
1. Utilize Advanced Control Systems
Modern injection moulding machines come with sophisticated control systems that allow for precise adjustments and monitoring. Utilize these features to:
- Fine-Tune Process Parameters: Adjust temperature, pressure, and injection speed to optimize the moulding process for your specific material and design.
- Monitor Real-Time Data: Track performance metrics such as cycle time, material usage, and machine status to identify areas for improvement.
2. Implement Predictive Maintenance
Predictive maintenance uses data analysis to predict when machine components are likely to fail, allowing for timely interventions. Implementing this approach involves:
- Installing Sensors: Equip your machines with sensors that monitor wear and tear on key components.
- Analyzing Data: Use data analytics to predict potential issues and schedule maintenance before problems occur.
3. Optimize Mould Design
The design of the mould plays a crucial role in production efficiency. To optimize mould design:
- Use Simulation Software: Employ mould flow simulation tools to analyze and optimize the mould design for better material distribution and fewer defects.
- Incorporate Cooling Channels: Design effective cooling channels to reduce cycle times and improve part quality.
4. Enhance Material Handling
Efficient material handling can significantly impact production efficiency. Consider the following:
- Automated Feeding Systems: Use automated systems to feed material into the injection unit, reducing manual handling and minimizing material waste.
- Proper Storage Conditions: Store materials in controlled environments to maintain their quality and prevent contamination.
5. Leverage Automation and Robotics
Integrating automation and robotics into your injection moulding process can enhance efficiency by:
- Automating Part Removal: Use robots to remove finished parts from the mould, reducing cycle time and minimizing manual labor.
- Implementing Automated Quality Control: Integrate vision systems and automated inspection tools to detect defects and ensure consistent quality.
6. Optimize Energy Consumption
Energy efficiency is a key factor in reducing production costs. To optimize energy consumption:
- Use Energy-Efficient Machines: Choose injection moulding machines with energy-saving features such as variable-speed drives and efficient heating systems.
- Monitor Energy Usage: Implement energy monitoring systems to track and manage energy consumption across your operations.
7. Conduct Regular Training for Operators
Well-trained operators are essential for maintaining production efficiency. Regular training ensures that your team can:
- Operate Machines Effectively: Understand and utilize the advanced features of modern injection moulding machines.
- Perform Routine Maintenance: Carry out basic maintenance tasks to prevent issues and ensure smooth operation.
8. Implement Lean Manufacturing Principles
Lean manufacturing principles focus on reducing waste and improving efficiency. Apply these principles to your injection moulding operations by:
- Identifying and Eliminating Waste: Analyze production processes to identify areas of waste, such as excess material usage or idle time.
- Streamlining Workflows: Optimize workflows to reduce setup times and improve overall efficiency.
Case Study: Successful Optimization in Action
To illustrate the impact of these optimization strategies, consider the following case study:
Company Profile
- Industry: Automotive Parts Manufacturing
- Challenge: High production costs and inconsistent part quality
Solution Implemented
- Advanced Control Systems: Implemented to fine-tune process parameters and monitor real-time data.
- Predictive Maintenance: Installed sensors and analyzed data to predict component failures.
- Automation and Robotics: Integrated robots for part removal and quality control.
Results Achieved
- Increased Efficiency: Reduced cycle times by 20% and minimized manual labor.
- Improved Quality: Achieved a 15% reduction in defects and increased overall part consistency.
- Cost Savings: Lowered energy consumption and maintenance costs, resulting in a 10% reduction in production costs.
Future Trends in Injection Moulding Technology
As technology continues to advance, several trends are expected to shape the future of injection moulding:
- Smart Manufacturing: Integration with the Internet of Things (IoT) and Industry 4.0 technologies for enhanced monitoring and control.
- Sustainable Practices: Increased focus on using recyclable materials and reducing environmental impact.
- Advanced Materials: Development of new materials with improved properties and applications.
Conclusion
Optimizing production efficiency with modern injection moulding machines involves leveraging advanced technologies, implementing strategic improvements, and staying informed about industry trends. By focusing on precise control systems, predictive maintenance, mould design optimization, and automation, manufacturers can significantly enhance their production processes. Embracing these strategies not only improves efficiency but also positions your business for success in the evolving manufacturing landscape of 2024.